Achieve Flawless Prototype with Aluminum Prototype Machining
Realizing Your Idea: An Overview of Aluminum Prototype Machining
A key component of product development is the aluminium prototype machining, which enables engineers and designers to transform ideas into real, working models. With so many advantages, this adaptable technique is the preferred option for a wide range of sectors, including consumer electronics, automotive, aerospace, and medicine.
This thorough manual delves deeply into the field of aluminium machining, examining its nuances, benefits, and uses. Regardless of your level of experience as a product developer or your stage in the design process, this post will provide you with the tools to make the most of this effective prototyping method.
What is Aluminum Prototype Machining?
CNC machines are used in aluminium prototype machining to produce three-dimensional models made of aluminium alloys. First, computer-aided design (CAD) software is used to produce a digital model (CAD model) of the prototype. After that, this digital blueprint is converted into a set of instructions for the CNC machine, which carefully manipulates cutting tools to remove material from a solid aluminium block, creating the prototype that is intended.
Various Industries Utilising Aluminum Prototype Machining Applications:
- Aircraft:
Aluminium is a common material option for aircraft prototypes because of its strength-to-weight ratio, which enables engineers to evaluate components’ performance in harsh environments.
- Automobile:
It is highly important in the automobile sector, enabling quick design validation and verification for everything from complex engine parts to lightweight body panels.
- Medical Devices:
Medical prototypes can benefit from the biocompatibility of several aluminium alloys. The functionality of prototypes may be thoroughly evaluated, guaranteeing the final device’s efficacy and safety.
- Consumer Electronics:
It contributes to the realisation of new consumer electronics, ranging from stylish smartphone casings to ergonomic laptop designs.
Selecting the Appropriate Aluminum Alloy for Your Model: An Effective Formula
The choice of the best aluminium alloy is the cornerstone of a successful aluminium prototype. For a prototype that fulfils your unique requirements, selecting the best alloy is as important as selecting the proper components for a delicious meal. To help you make an educated choice, this article explores the important aspects to take into account while traversing the wide world of aluminium alloys for prototyping.
Understanding the Balancing Act:
The compelling combination of qualities that aluminum alloys offer makes them perfect for a wide range of prototype applications. But because every alloy has a different set of advantages and disadvantages, choosing one requires thorough consideration of the pros and cons. The following are the main things to consider:
- Strength:
The necessary strength for your prototype is an unavoidable requirement. Alloys with outstanding strength-to-weight ratios like 7075 are the preferred option for prototypes meant to bear heavy loads or pressures. On the other hand, applications that prioritise lightweight designs could prefer alloys like 6061 because they have a strong strength-to-machinability ratio.
- Weight:
In several sectors, including consumer electronics and aircraft, reducing weight is crucial. Choosing lighter alloys, such as 5052 or 6061, becomes crucial in these situations. These alloys reduce weight in the prototype without sacrificing the necessary functionality.
- Machinability:
The speed and expense of prototyping are greatly influenced by the ease with which an alloy can be machined. Compared to less machinable alloys, more machinable alloys, such as 6061, allow for quicker and more economical machining. Machinability must be prioritised if complicated geometries or intricate features are needed.
- Corrosion Resistance:
This becomes an important consideration for prototypes that are going to be used in severe settings or that are going to be exposed to moisture. For these kinds of uses, alloys with exceptional corrosion resistance, like as 5052, are ideal. Selecting the most corrosion-resistant alloy for your prototype will be made easier if you know what kind of environment it will be operating in.
Beyond the Basics: Additional Considerations
Although the fundamental elements discussed above serve as the basis for your alloy choice, you should also take the following into account:
- Heat Treatment:
To improve the mechanical qualities of some aluminium alloys, such as strength and hardness, heat treatment can be used. Think about alloys that react well to heat treatment procedures if these characteristics are essential for your prototype.
- Surface Finish:
Your choice of alloy may be influenced by the intended surface finish of your prototype. While certain alloys may require further surface treatments, others are better suited for obtaining a polished, smooth finish.
- Availability and Price:
Depending on your area and supplier, there may be differences in the availability and price of certain aluminium alloys. Budgetary restrictions should be taken into consideration while making your ultimate decision, even if price shouldn’t be the only consideration.
The Benefits of Machining Aluminum Prototypes: An Activator for Product Innovation
A key component of the product development process is the aluminium prototype machining, which enables engineers and designers to close the gap between ideas and physical reality. This adaptable method has several advantages and advances projects quickly, precisely, and functionally. Let’s examine in more detail the main benefits that make machining aluminium prototypes such an effective tool:
- Unmatched Dimensional Accuracy:
The process of creating aluminium prototypes, CNC machining, is known for its extraordinary precision. Prototypes that closely mimic the final product design result from this, guaranteeing a smooth transition from prototype to production. For items that require tight tolerances or have complicated features, dimensional precision is crucial. This crucial feature is provided by aluminium prototype machining, which makes it possible to carefully verify and validate design parameters.
- Material Flexibility: A Match for Diverse Needs
The wide range of aluminium alloys available to you is a distinguishing feature of aluminium machining. This broad selection of materials meets a variety of project needs. Do you need a prototype that can withstand extreme strain for severe testing? Alloys such as 7075 offer the required strength. Maybe losing weight should be your priority. Weight-sensitive applications can be better served by the prototype by utilising lighter alloys like 6061. It provides a thorough investigation of appropriate aluminium alloys for different types of prototype requirements.
- Quick Prototyping: Accelerating the Innovation Cycle
In today’s fast-paced world of product development, time is critical. When it comes to providing a substantially faster turnaround time than conventional production processes, aluminum prototype excels. This speed enables you to efficiently iterate designs, bring concepts to life, and obtain insightful input from stakeholders as soon as possible. Aluminum prototype machining shortens the duration of the prototyping phase, which speeds up the entire product development cycle and gives you a market advantage.
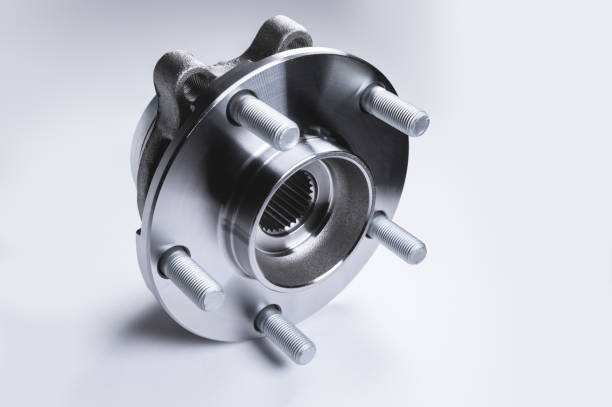
Why is aluminum prototype machining important?
There is no denying the importance of manufacturing aluminium prototypes. This method gives product creators the resources they need to realise their ideas, from great dimensional precision and material variety to quick prototyping speeds and functional testing possibilities. Utilising aluminium prototype machining’s capabilities may help you guarantee product quality, expedite the development process, and obtain a competitive edge in the market.
- Functional Prototypes: Beyond Aesthetics, Towards Real-World Performance
Prototypes made of aluminum are more than simply pretty pictures. Functional testing may be done with aluminum because of its inherent strength and workability. Before committing to full-scale manufacturing, this allows you to assess the prototype’s performance under actual conditions, perhaps revealing design faults or areas for improvement. Because it may be used for functionality testing, aluminum prototype machining is a highly useful tool for making sure your final product is reliable and effective.
- Simplifying the Road to Perfection through Design Iteration:
The versatility of aluminium prototype is what makes it so beautiful. It is easy to incorporate changes into the prototype design, which facilitates rapid modifications and improvements. With this flexibility, you can quickly experiment with several design iterations and refine the prototype until it performs better than you had imagined. To achieve design quality and maximise product usefulness, this iterative process—which is made possible by aluminium prototype machining—is essential.
Streamlining Innovation: The Prototype Design Process Explained
Thorough planning is necessary to pave the way from conception to creation. A clearly defined design process is essential for aluminium prototype machining since it facilitates the effective conversion of concepts into physical prototypes. Let’s examine the crucial actions involved:
- Concept Development:
The creative spark is ignited at this first stage. Conceptual sketches and brainstorming sessions help to clarify the main features and general design approach of your product.
- 3D CAD Modelling:
In this stage, the idea design becomes more tangible. A comprehensive 3D CAD model is created using specialised software, and this model serves as the CNC machining process blueprint.
- Design for Manufacturability (DFM):
It is an important but sometimes disregarded stage. To make sure the CAD model is compatible with CNC manufacturing, it is carefully examined. It may be necessary to make minor changes to the design to maximise manufacturing efficiency and cost.
- Manufacturing prototypes:
The last stage of the design process. The CNC machining programme is created using the completed CAD model. To construct the actual prototype, the machine is fitted with cutting tools that carefully remove material while maintaining the desired aluminium alloy.
- Prototype Finishing:
To get the appropriate looks and performance, the unfinished machined prototype may go through further finishing procedures like sanding, polishing, or anodizing.
Conclusion:
Equipped with cutting-edge technology, the HuaYu Prototype team of professionals specialises in handling complex designs and exacting aesthetic requirements. We provide a broad range of on-demand manufacturing services that are intended to meet different needs.