Automotive CNC Machining: The Powerhouse Behind Your Car
Revolutionizing the Automotive Industry: The Power of Automotive CNC Machining:
The automobile sector is driven by innovation and is always pushing the limits of efficiency, performance, and design. Automotive CNC Machining is a potent technology at the centre of this growth. This accurate and adaptable method is revolutionizing the production of auto parts by making it possible to create complex parts, achieve tight tolerances, and propel improvements throughout the automotive industry.
Innovation is key to the automobile industry, and CNC machining is at the forefront of this innovation. From lightweight composites to vintage engine blocks, complex parts with strict tolerances may be produced thanks to this exact technique. Unmatched accuracy, material diversity, and the capacity to work with intricate geometries are all provided by CNC machining. Faster development cycles, lighter cars, and efficient engines are the results of this. The future of automobile production will be shaped by the further evolution of CNC machining as the industry adopts electrified vehicles and autonomous driving.
Understanding CNC Machining for Automotive Applications:
CNC (Computer Numerical Control) machining carefully shapes a piece of material into the required shape by using computer-controlled equipment to carry out pre-programmed toolpaths. This translates to outstanding precision and reproducibility in the context of automobile parts, enabling the production of precise features, complicated geometries, and components with minuscule tolerances.
Benefits of Automotive CNC Machining: A Multifaceted Advantage:
There are several benefits of incorporating CNC machining into the car production process.
- Unmatched Precision:
The manufacturing of parts that satisfy strict automotive criteria is made possible by the extraordinary precision that CNC machining promises. Precise measurements guarantee smooth assembly, peak efficiency, and improved engine performance.
- Material Versatility:
CNC machines are capable of working with a large variety of materials, including lightweight composites like carbon fiber and conventional metals like steel. Because of this adaptability, producers may choose the best material for each component, maximizing performance, strength, and weight.
- Complexities Made Simple:
Intricate forms and geometries that would be difficult or impossible to accomplish using conventional methods are expertly produced with CNC machining. This creates opportunities for creative designs, enhanced functionality, and internal weight reduction.
- Rapid Prototyping:
The design and development process is streamlined by the capacity to swiftly produce prototypes using CNC machining. The effective testing and refinement of concepts by engineers can expedite the time-to-market for novel vehicles and technology.
- Cost-Effectiveness:
CNC machining is more affordable than traditional techniques like casting or forging for bespoke items or low-volume manufacturing runs. This makes it perfect for speciality applications, high-performance vehicle customisation, and the restoration of historic cars.
- Scalability and Repeatability:
Automotive CNC machining can be easily scaled up to meet production needs, allowing for a smooth transition from high-volume manufacturing to low-volume prototyping. Every single item that is made has constant quality because of the inherent repeatability.
The Evolving Landscape: Embracing Innovation in Automotive CNC Machining:
There is still more to be seen in the automobile CNC machining success story. With the industry rapidly moving towards an electric car and autonomous driving future, this adaptable technology is certain to see even more developments.
- Light weighting for Electric Dominance:
Optimizing range is a major issue for electric cars. CNC machining takes over here. Achieving this aim will depend in large part on our capacity to accurately design components out of lightweight composites like carbon fiber. An important aspect driving customer acceptance of electric vehicles is their longer range, which is a result of lighter automobiles.
- 5-Axis Machining:
Although 3-axis CNC machining has been a powerful tool, 5-axis machines are the way of the future. These sophisticated technologies provide unmatched mobility, enabling the development of ever more complex shapes. This creates opportunities for creative designs, internal weight-reduction features in components, and maybe whole new features in cars of the future.
- Sustainability Takes the Moment:
Being environmentally sensitive is no longer a side issue. Sustainable methods are essential for the car manufacturing industry of the future. Energy usage and waste production may be minimized by CNC machining optimization. This might entail using recyclable materials, developing novel toolpath methods, and energy-efficiently optimizing cutting settings. CNC machining may help create a more environmentally friendly automobile sector by adopting these methods.
This CNC machining is a major force behind innovation in the automobile industry and goes beyond simple manufacturing. CNC machining will keep developing as the sector embraces the future, providing answers for lightweight, enabling cutting-edge designs, and blending in perfectly with environmentally friendly procedures. The vehicles of the future will be shaped by this potent technology.
HuaYu prototype: Your Partner in Automotive CNC Machining Excellence:
HuaYu Prototype is positioned as a trustworthy partner for your automobile CNC machining needs in this conclusion, which highlights the forward-thinking aspect of CNC machining. It also includes a call to action to entice visitors to get in touch with your business. We are aware of the vital role CNC machining plays in the automotive sector. We have a group of talented engineers, cutting-edge CNC equipment, and an unwavering dedication to quality that goes above and beyond industry norms.
HuaYu prototype is your reliable partner whether you need a low-volume prototype for a custom automotive project high-volume manufacturing of intricate engine components, or everything in between. Get in touch with us right now to talk about your unique requirements and find out how our knowledge of CNC machining can support your car projects.
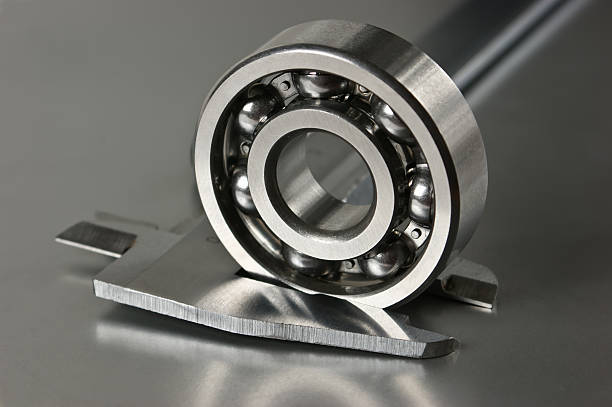
From Powerhouses to Showpieces: The Diverse Applications of Automotive CNC Machining:
There is more to CNC machining than meets the eye in the car manufacturing industry. Because of its adaptability, it may be used to create a wide range of components, from the engine’s core to the external features.
- The Workhorses of the Engine:
The most important parts of an automobile’s beating heart are machined with a CNC machine. Engine blocks are meticulously molded using CNC, complete with elaborate oil channels and water jackets. Cylinder heads benefit from CNC’s ability to manufacture complicated forms and smooth surfaces since they need tight tolerances for effective combustion. The strength, accuracy, and precise features of crankshafts, camshafts, pistons, and connecting rods are all attributed to CNC machining.
- Beyond the Engine Bay:
The capabilities of automotive CNC machining go much beyond the engine. Gears, shafts, and differentials are examples of transmission components that depend on CNC for accurate meshing and seamless functioning. CNC machining is a great option for suspension parts as it can create sturdy and lightweight elements like control arms and knuckles, which are essential for handling. CNC machining also benefits braking systems, since rotors and calipers are painstakingly made for maximum stopping power and weight reduction.
- Customization Takes the Wheel:
CNC machining is essential to the high-performance modification and car restoration industries. CNC machining ensures authenticity and preserves automotive history by making it possible to recreate difficult-to-find or discontinued parts for antique automobile repair. CNC machining enables the production of lightweight, highly durable bespoke parts like intake manifolds, camshafts, and pistons for high-performance cars, pushing the limits of both performance and customization.
- Suspension Components:
CNC machining is used in control arms, knuckles, tie rods, and other suspension elements to provide lightweight designs without sacrificing strength.
- Brake Systems:
To provide remarkable stopping power and weight savings, brake callipers, rotors, and other braking components can be CNC-machined.
The Material Matchmaker: Optimizing Automotive Parts with CNC Machining:
The materials that automotive CNC machining sculpts are just as magical as the technology. Selecting the appropriate material for every part is essential to obtaining the best possible performance, minimizing weight, and saving money. Let’s examine some of the essential materials used in CNC machining of automobiles:
- CNC machining of aluminum:
Aluminum is a versatile material that combines exceptional strength-to-weight ratio, outstanding machinability, and lightweight characteristics. Aluminum’s full potential may be realized through CNC machining, which makes it possible to construct complex engine parts like intake manifolds and cylinder heads. This results in better overall vehicle performance and fuel economy.
- Steel CNC Machining:
Steel is unmatched in terms of strength and durability. With the use of CNC machining, steel components with extreme pressure and stress tolerance may be precisely shaped. Steel’s strength is frequently utilized by crankshafts, axles, and suspension parts, which are CNC-machined to exact tolerances and maximum performance.
- Composite CNC Machining:
Composites, such as carbon fiber, are the way of the future in vehicle production. These cutting-edge materials push the limits of lightweight design with their remarkable strength-to-weight ratios. For components like body panels and chassis pieces, CNC machining is essential for accurately shaping these composites, which results in a noticeable weight reduction and increased fuel economy.
Conclusion:
HuaYu Prototype is your reliable source for complete automobile CNC machining solutions. We take your idea and turn it into a reality, leading your project through the prototype stage and low-volume manufacturing with ease. Our dedication toward our products is accuracy and quality guarantees reliable, high-performing products that adhere to your particular requirements.