CNC Prototype Machining: Bring Your Vision to Life
Bringing Your Vision to Life: A Guide to CNC Prototype Machining
It’s a thrilling process to get from a conceptual notion to a physical product. However, prototyping is an essential way to evaluate your idea before going into full-scale production. This is where CNC prototype machining comes in, providing an effective and accurate way to make prototypes that are both aesthetically pleasing and useful. This thorough manual delves deeply into the field of prototype machining, examining its fundamental procedures, benefits uses, and important factors. Regardless of your level of experience as an engineer or your aspirations as an entrepreneur, this knowledge will enable you to make full use of CNC machining for your next project.
Understanding CNC Prototype Machining
As a subtractive manufacturing technique, CNC machining carefully removes material from a solid block to get the required end shape. In essence, they are computer-controlled robots that use a variety of cutting tools and precise motions in response to a digital design (CAD model). High-fidelity prototypes may be produced with great precision and reproducibility because of this degree of automation. For prototypes, CNC machining is mostly done in two ways:
- CNC milling:
This adaptable method uses rotating cutting tools to chisel intricate shapes into the material. It works well for forming components with several planes, pockets, slots, and complex features.
- CNC Turning:
To produce desired forms, material is removed by rotating cylindrical workpieces while a fixed cutting tool is in place. It is particularly good at making prototypes of rotationally symmetric items like gears, bushings, and shafts.
Advantages of CNC Prototype Machining
When it comes to advantages over other prototype techniques, CNC prototype machining is quite appealing.
- High Precision and precision:
It ensures that your prototypes closely match the final product by providing remarkable dimensional precision and repeatability.
- Broad Material Compatibility:
A wide range of materials, including plastics, wood, and metals (brass, steel, and aluminium), may be machined using CNC technology. With a more realistic prototype thanks to its adaptability, you may match the qualities of your planned production material as precisely as possible.
- Operational Models:
In contrast to certain additive manufacturing techniques, such as 3D printing, CNC machining generates sturdy, useful prototypes that possess the same strength and performance attributes as the final product. This makes it possible to validate and test design functionality thoroughly.
- Rapid prototyping:
With more straightforward designs, modern CNC machines can create prototypes rather quickly. Your product development cycle is accelerated by this quick response time.
- Design for Manufacturability (DFM):
Early in the development phase, CNC machining’s subtractive nature makes it the perfect tool for spotting any manufacturability-related design faults. This enables design modifications before the start of mass production.
CNC Prototype Machining Applications
Several industries use CNC prototype machining because of its adaptability and capacity to produce working products. Here are a few well-known applications:
- Aerospace:
Exact machining of materials such as titanium and aluminium is necessary for the prototyping of lightweight, high-strength components for aircraft and spacecraft.
- Automotive:
The precision and material compatibility of this machining is advantageous in the development of working prototypes for engine parts, gearboxes, and other essential components.
- Medical Devices:
They can provide the exact dimensions and biocompatible materials needed to create prototypes for prostheses, surgical instruments, and other medical equipment.
- Consumer electronics:
It is ideally suited for the intricate features and strict tolerances that are frequently involved in prototyping housings, brackets, and other components for electrical gadgets.
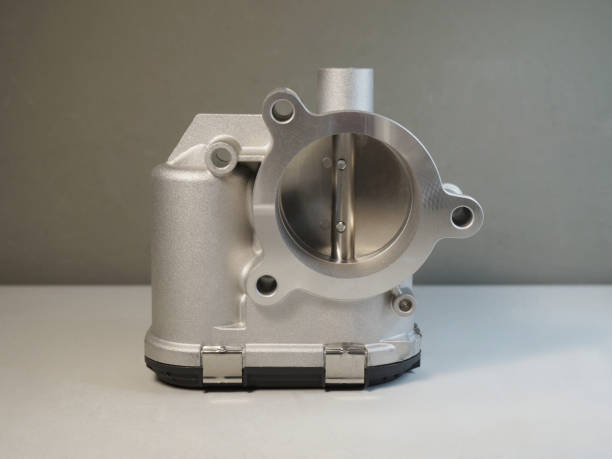
Important Things to Think About When Machining CNC Prototypes
Before starting your prototype machining project, keep the following important things in mind:
- Complexity of your design:
The degree of geometric complexity and intricacy in your design will determine whether to use a CNC milling or turning operation, which may affect the final cost.
- Material Selection:
It’s crucial to choose the right material for your prototype. It should take into account machinability for CNC procedures and align with the required functionality and attributes of the finished product.
- CNC Tolerances in Machining:
The acceptable departure from the given measurements is referred to as tolerance. The necessary degree of accuracy will establish the parameters for the machining process and may affect the expense.
- Cost:
Several factors, including material selection, design complexity, turnaround time needed, and machining volume, affect the cost of CNC machining.
CNC Machining Tolerances for Prototypes: Striking the Right Balance
CNC machining is an effective technique for producing high-quality prototypes, but it takes knowledge of CNC machining tolerances to get the required degree of precision. The allowable departure from the given dimensions in your CAD model is defined by these tolerances. The usefulness, cost, and overall success of your prototype are all directly impacted by the tolerance you choose.
Why Tolerances Matter for Prototypes:
- Functionality:
Close tolerances guarantee that the fit and functionality of your prototype precisely correspond to the finished product. This enables thorough testing and the detection of any possible design defects before large-scale manufacturing.
- Cost:
Precise machining techniques are necessary to achieve tighter tolerances, which frequently raises costs. Finding the ideal balance between usefulness and tolerance, however, can save expensive redesigns or revisions in the future.
- Material Selection:
Achievable tolerances are affected by the machinability of various materials. Choosing a material that can be machined to the required degree of accuracy is ensured when tolerances are discussed with your CNC machining partner early on.
Tips for Choosing Tolerances:
- Determine Critical Dimensions:
Concentrate on attaining close tolerances for dimensions that are essential to the assembly and operation of the item. Tolerances might be looser in less important sectors.
- Speak with your partner for CNC machining:
Talk to your CNC machining provider about the specifications of your project and the tolerances you require. Their knowledge may assist you in striking the best possible compromise between accuracy and economy.
You may make wise judgements for your prototypes that will ensure functionality, economy, and a smooth road to successful product development by being aware of CNC machining tolerances.
Picking the Perfect Fit: Best Materials for CNC Prototyping
Choosing the appropriate material for your CNC prototype is an essential step that will impact its overall success, usefulness, and appearance. This article examines some of the top materials for CNC prototyping, taking into account aspects such as characteristics, applicability for certain applications, and machinability.
Factors to Consider When Choosing a CNC Prototyping Material:
- Machinability:
The degree to which a material may be worked by CNC procedures without difficulty. Most metals, such as brass and aluminium, are easily machined, while certain tougher materials may need specific tools.
- Material Properties:
Take into account how you want your finished product to work. Selecting a prototype material that has qualities such as strength, weight, heat resistance, and corrosion resistance is important.
- Application:
The materials you choose for your prototype will depend on its industry and intended use. For example, consumer electronics prototypes may prioritise aesthetics above utility, whereas aerospace prototypes may require lightweight, high-strength materials.
Additional Considerations:
- Functional Prototypes vs. quick Prototyping:
Machinability and affordability may be the main considerations for quick prototypes that emphasise visual representation. Choosing a material that closely resembles the finished product is essential for functional prototypes that need certain qualities.
- Options for Finishing:
Anodizing, polishing, or painting are a few finishing methods that may be used after CNC machining. When choosing your material, keep the intended final appearance and utility in mind.
You may select the ideal material for your CNC prototype by being aware of these aspects and the characteristics of various materials. This guarantees that your prototype fulfils its intended function and prepares the path for a smooth transition to large-scale manufacturing.
Unveiling the Costs: Factors Affecting CNC Prototype Machining
A strong tool for verifying your design is cnc prototype machining; but, to make an educated choice, you must be aware of the associated costs. The following is a summary of the major factors influencing the cost of your CNC prototype:
- Material Selection:
An important consideration is the cost of materials. those that are rare or more difficult to process, like titanium, will cost more than those that are easily accessible, like aluminium.
- Complexity of Design:
Higher prices result from the need for more specialised tools and more machining time to complete intricate designs with many features, tight tolerances, and sharp corners. In general, simpler designs are more economical.
- Machining Time:
The cost is directly impacted by the amount of time it takes to manufacture your prototype. Longer machining durations are frequently required due to complex designs and strict tolerances.
- Quantity:
Compared to making a small batch, prototyping a single device usually costs more per piece. Higher volumes trigger economies of scale, which lower the cost per unit.
- CNC Machining Technique:
CNC turning works well for rotating parts, but CNC milling is more adaptable for complicated geometries. Milling may be a little more expensive because of its intricacy.
- Finishing Options:
The total cost rises when post-machining finishes like anodizing or polishing are included. Determine whether they are necessary for the function of your prototype.
Conclusion:
HuaYu Prototype is skilled in taking your product concepts from early prototypes to mass manufacturing. Equipped with cutting-edge technology, our team of professionals is skilled in handling complex designs and exacting aesthetic requirements. We provide a broad range of on-demand manufacturing services that are intended to meet different needs.