Mastering Design for CNC Machining: Your Guide to Flawless Parts
Mastering CNC Machining Design: Your Hands-On Guide to Perfect Part Creation
When it comes to producing intricate parts, the field of CNC machining provides unmatched versatility and precision. However, it is essential to comprehend the design for CNC machining to fully utilize CNC. It ensures that your designs flow naturally into the world of CNC by bridging the gap between design and manufacture. With the help of this thorough guide, which delves deeply into DFM principles, you will be able to design faultless parts that are optimized for CNC machining.
Design for Manufacturability (DFM): An Understanding
DFM is a proactive design methodology that takes manufacturing viability into account right from the start. It entails evaluating the design in light of CNC machining capabilities, identifying any obstacles, and refining the design to ensure successful and economical production.
Unleash CNC Machining’s Power: The Secret Weapon – Design for Manufacturability (DFM)
Although CNC machining offers remarkable accuracy and adaptability, design for manufacturability (DFM) is your secret weapon if you want to fully realize its potential. It facilitates the seamless transition from design to perfectly machined parts by acting as a link between your vision and the world of CNC. Here’s how DFM enables you to work at your best and maximize efficiency:
- Cost savings:
DFM assists in identifying design elements that result in excessive material waste or necessitate intricate machining procedures. One way to cut production costs dramatically is to optimize your design from the start. DFM makes your manufacturing process leaner and more economical by reducing material consumption and the requirement for rework.
- Faster Turnarounds:
By anticipating possible machining issues before production starts, it optimizes the entire process. Lead times are shortened as a result of the elimination of rework and delays. Receive your parts more quickly and finish the project more quickly.
- Improved Quality:
DFM assists you in creating parts that are best suited for CNC cutting. This results in components with reduced defect risk, better surface finishes, and improved dimensional accuracy. Every time, DFM guarantees consistent, high-quality products by averting possible machining problems.
- Design Efficiency:
DFM promotes a design approach that takes manufacturability and utility into account. This results in more effective designs that are easier and less expensive to produce in addition to being practical. Maximize functionality through a more efficient design approach.
You can get a potent combination of cost reductions, quicker turnaround times, improved quality, and a more efficient design process by incorporating DFM into your design workflow. This gives you the confidence to realize your ideas since you know they can be transformed into perfect, finely machined CNC parts.
Fundamentals of CNC Machining Design
When creating for design for CNC machining, keep the following important guidelines in mind:
Section Geometry:
- Reduce Complexity:
Whenever feasible, go for more straightforward geometry. Steer clear of complex features that call either specialist tooling or multi-axis machining.
- Dimensions and Orientation of Features:
Take into account the dimensions and alignment of slots, pockets, and holes. Make sure the features are positioned to allow for appropriate tool access and are large enough to accommodate machining equipment.
- Wall Thickness:
To prevent deflection or breaking during machining, keep the part’s walls thick enough and consistently throughout.
- Draft Angles:
To make mould release easier and avoid tool scraping during machining, incorporate draft angles into vertical walls.
Selection of Materials:
- Machinability:
Select materials that are compatible with CNC cutting. Think about things like tool wear potential, chip formation, and machinability ratings.
- Material Availability:
The design should also take the cost and availability of the material into consideration.
Tolerances and Surface Coatings:
- Define Tolerances Clearly:
To put it, on your design, indicate tolerances for all important dimensions. More accurate machining will be needed to achieve tighter tolerances, which could raise costs.
- Possible Surface Finishes:
Indicate what surface finishes are realistically possible given the selected material and machining method. Strive for a cost-effectiveness and functionality balance.
Advanced Design Considerations for CNC Machining: Going Beyond the Fundamentals (DFM)
Although understanding the fundamentals of DFM is essential, there are a few more things that improve your design for smooth CNC machining:
- Machining Procedures:
CNC machining provides a range of procedures with advantages. You can customize your design by being aware of the capabilities of turning, milling, and multi-axis machining. For example, multi-axis machining may be required for intricate interior details, while milling may be a better option for simpler items.
- Tooling and Fixturing:
Think about the equipment and fixtures required to hold your component firmly while it is being machined. Make sure all features are properly accessible to tools, and steer clear of circumstances where the fixture itself impedes machining. Toolpaths may be seen using software simulations, and potential fixture collisions can be detected.
- Post-Processing:
Following CNC machining, not every part is completed. It can be necessary to do surface finishing, heat treatment, and deburring. To prevent surprises later, account for these post-processing stages while designing. Permitting marginally larger features, for instance, can facilitate material removal during post-processing procedures like polishing.
- Design for Automation:
If you want to produce large quantities of work, think about including design elements that make handling and assembly more automated. This could entail adding chamfers for simpler robotic handling or standardizing hole diameters.
- It’s All About Communication:
It’s critical to keep lines of communication open with your CNC machining partner during the design phase. Feedback on your design’s manufacturability and possible cost optimizations can be obtained by sharing it early.
Adding these cutting-edge factors improves your design for CNC machining. This guarantees a seamless transfer from the prototype to the completed product, reducing manufacturing lead times and optimizing effectiveness.
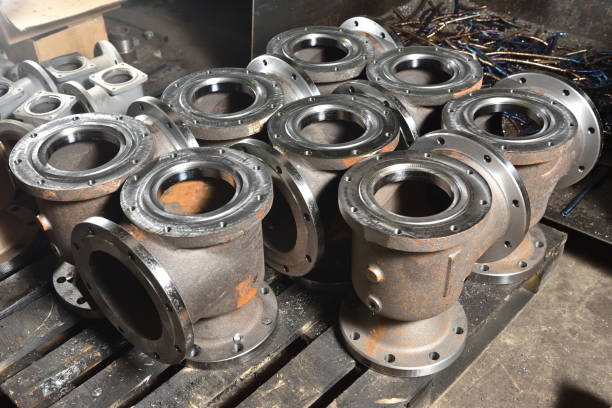
Unleashing Potential: CNC Machining Applications of Design (DFM) Across Industries:
Design for CNC machining, or DFM, is more than just an idea; it’s a potent instrument with uses in a wide range of sectors. The full potential of CNC machining can be realized by incorporating DFM concepts, which can lead to:
- Enhanced Prototyping:
It enables high-accuracy, quick prototyping of intricate parts. This speeds up development, simplifies the design process, and aids in the early detection of possible problems. Imagine producing complex prototypes for medical devices or aerospace parts that are CNC-optimized and prepared for testing.
- Precision Manufacturing:
It makes certain that designs are suited for particular CNC operations, such as turning, milling, or multi-axis machining. This results in precise parts with tight tolerances, perfect for use in demanding medical devices, high-performance machinery parts, and automotive components, among other applications.
- Production at a Low Cost:
It assists in getting rid of design elements that need a lot of material waste or intricate machining. In sectors like consumer electronics, where even modest cost reductions can have a big impact, this equates to huge cost savings.
- Efficiency through Lightweighting:
It enables the creation of parts that are both robust and lightweight. This is especially important in the aerospace industry, as reduced weight results in increased fuel economy. Envision creating an aircraft wing that is lightweight and maximizes performance through CNC machining.
- Better Product Performance:
It contributes to the design of parts with better surface finishes and dimensional accuracy by taking manufacturing feasibility into account. In sectors like robotics, where precise movement and close tolerances are crucial, this improves product performance.
In addition to these fundamental uses, DFM supports the following sectors:
- Medical Devices:
Manufacturing surgical instruments or biocompatible implants with exact shapes and high surface finishes.
- Consumer goods:
Creating visually appealing, cutting-edge designs that are economical to produce with CNC.
- Defence:
Creating components that are CNC-produced with maximum strength and dependability for use in military applications.
Accepting DFM opens up a whole new realm of possibilities of design for CNC machining. With the help of this strategy, companies in a variety of sectors may produce better outcomes, work more efficiently, and confidently realize their ideas. Utilizing DFM concepts allows you to maximize CNC machining’s capabilities. HuaYu Prototype is your collaborator in producing perfect components. Get in touch with us right now to talk about your project and discover the advantages of CNC machining powered by DFM.
Design Software Tools for CNC Machining
Several CAD (Computer-Aided Design) software packages are tailored to DFM concepts. These instruments provide functions such as:
- Checks for Design for Manufacturability:
Find possible problems with the CAD software’s ability to be manufactured.
- Simulations of machining:
By virtually seeing the CNC machining process, you may spot possible issues before production starts.
- Combining with CAM software:
Errors are decreased and workflow is streamlined when CAD and computer-aided manufacturing (CAM) applications are seamlessly integrated.
Conclusion:
You may realize CNC machining’s full potential by adhering to DFM principles. Leading supplier of design for CNC machining services, HuaYu Prototype, has a wealth of experience and knowledge in assisting customers in turning their designs into precision CNC machined parts. You can ensure the effective execution of your design vision, accomplish efficient production, and reduce costs by adopting a DFM-centric strategy.