Prototype CNC Machining: The Fast, Precise Way to Bring Your Ideas to Life
Understanding the Different Purposes of Prototype CNC Machining
Prototype cnc machining has a variety of uses throughout developing a product. Prototypes that are customized to meet particular demands can be made with CNC machining:
Functional prototypes:
They are employed to evaluate the components’ assembly, fit, and mechanical performance. CNC machining is excellent at producing extremely accurate and dimensional items from a variety of materials, which makes it ideal for developing functioning prototypes.
Appearance Prototype CNC machining:
These prototypes aim to imitate the final product’s appearance and feel. They are perfect for marketing, user testing, and design validation. Realistic prototypes may be made using CNC machining because they can provide outstanding surface finishes on a variety of materials.
Rapid prototyping CNC machining:
When it comes to quick prototypes, time is of the essence. When it comes to producing prototypes, CNC machining is more expedient than more conventional techniques like manual milling. Time-to-market and design iterations can be accelerated as a result.
Prototyping is not the only application for CNC machining. Additionally, it can be used for the limited-edition, short-run fabrication of parts. Producing parts for specialized applications or verifying market demand might both benefit from this.
Low volume production CNC machining:
Highlighting the Material Versatility of Prototype CNC machining:
The fact that CNC machining is compatible with a wide range of materials is a major benefit:
Metals:
Working with a variety of metals is a perfect application for CNC machining. This makes it possible to create sturdy, useful prototypes that are appropriate for demanding applications.
Plastics:
A large variety of Plastics, including high-performance engineering thermoplastics like ABS and polycarbonate, are capable of being CNC machined. This makes it possible to develop prototypes that closely resemble the material qualities of the finished product.
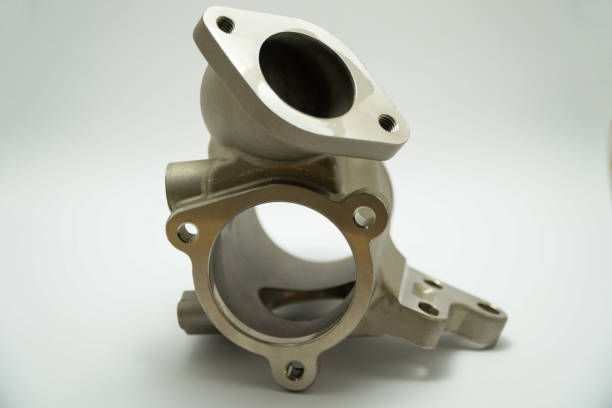
Considering Turnaround Time for Prototype CNC Machining Projects:
The following variables affect how quickly a prototype CNC machining job may be completed:
- Design complexity:
It is normal for more complex designs with strict tolerances to take longer to manufacture.
- Material selection:
Lead time may be impacted by the need for specific machining procedures for some materials.
- Workload in the shop:
Turnaround times may be impacted by the CNC machining service’s capability.
Targeting Specific Industries with Prototype CNC Machining
Because of its adaptability, CNC machining is a useful tool in a variety of industries:
- Aerospace:
Lightweight and highly precise components are required for the aircraft sector. Accurate prototypes made of materials like titanium and aluminum may be created by CNC machining and subjected to rigorous testing.
- Automotive:
CNC machining is essential to the automobile sector, from concept cars to working prototypes for new vehicle components. It’s perfect for reproducing finished items because it can work with a variety of metals and polymers.
- Medical equipment:
Biocompatibility and stringent quality control are necessary for medical equipment. Since CNC machining produces accurate and consistent results, it may be used to prototype implants and medical equipment using the right materials.
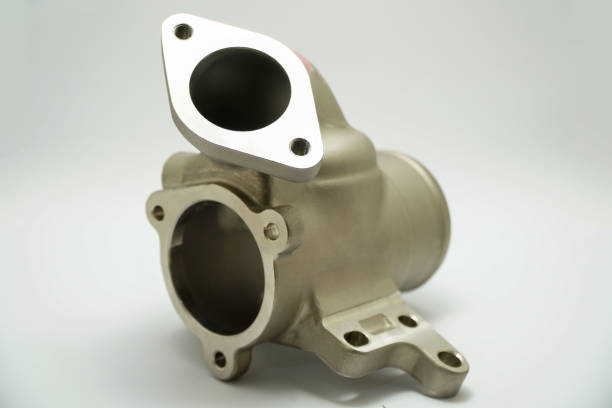
Benefits of CNC Machining for Low-Volume Production Prototypes:
Although CNC machining is typically connected with prototypes, it also presents a strong option for low-volume production runs. This ideal location between custom prototypes and large-scale production has the following benefits:
- Cost-Effectiveness for Limited Quantities:
CNC machining reduces the requirement for pricey tooling as compared to conventional mass production techniques like injection molding or die casting. This makes it an affordable choice for small-batch production, particularly in the early stages of production or for specialized uses.
- Flexibility for Design Iteration:
Rapid design modifications and alterations are possible when using CNC machining in low-volume production. This adaptability is essential for fine-tuning your product before committing to a bigger production run, based on input from users or test results.
- Faster Time-to-Market:
CNC machining enables you to swiftly create a limited amount of components with less setup time than traditional production processes. This results in a quicker time to market, allowing you to test your product earlier and obtain insightful market data.
- High-quality parts:
The accuracy and consistency of CNC machining are well known. This guarantees that consistent, high-quality components that satisfy your design standards are produced even during low-volume manufacturing runs.
- Material Versatility:
As previously shown, a variety of materials, including metals, polymers, and even wood, may be machined using CNC technology. With this flexibility, you may manufacture low-volume components for functional testing and validation that closely resemble the material qualities of the finished product.
- Bridge to Full-Scale Production:
Prototyping and full-scale manufacturing may be connected effectively with low-volume production using CNC machining. Before ramping up production, it enables you to test the design, spot any possible problems, and improve your product. Check out our website Prototype to Production with CNC Machining for an example of how CNC machining helped a company swiftly bring their unique product to market.
Choosing the Right Materials for CNC Machined Prototypes:
For your prototype CNC machining to be successful overall and to perform well, you must use the best material. Here is a summary of the important things to think about before choosing:
Knowing the Goal of Your Prototype:
Functional Prototypes: Elasticity, weight, and resilience to wear and tear are the most important parameters for prototypes that prioritize functionality. Think about resources such as:
Metals: Steel (great strength and durability), Aluminum (strong and lightweight), and Stainless Steel (strong and resistant to corrosion).
Polycarbonate (strong impact resistance) and Nylon (excellent wear resistance and dimensional stability) are examples of engineering plastics.
Material Properties:
Machinability: The ease with which a material can be machined varies. Reduced costs and quicker turnaround times are two benefits of easier machinability. Think about the trade-off between the desired material qualities and machinability.
Weight and Strength: Metals like titanium or aluminum may be the best choice for prototypes that need to be lightweight or have great strength. Weight and strength may be balanced using plastics, although wood works well in low-stress situations.
Durability and Wear Resistance: Take into account the anticipated deterioration of your prototype. Stainless steel and several engineering plastics are examples of materials with exceptional wear resistance and durability.
Heat Resistance: Select a material with good thermal qualities if your prototype will be subjected to high temperatures. Certain high-performance polymers can tolerate high temperatures; however aluminium has outstanding heat dissipation.
Chemical Resistance: Use a material that has the right amount of chemical resistance for prototypes that will be exposed to solvents or chemicals. Stainless steel and several polymers are excellent in this regard.
Aesthetics and Finishing:
Colour and Texture: Take into account the intended color and texture of the finished product while creating appearance prototypes. While certain materials may be painted or treated to obtain the required aesthetics, others give a limited selection of colors.
Surface Finish: Surface finishes ranging from rough to smooth and polished can be produced using CNC machining. The choice of materials should consider the intended finish since certain materials work better with particular finishes.
How to Design Prototypes for CNC Machining: Optimizing for Success?
Its full potential may be realized by designing a prototype especially for CNC machining, which produces more precise, useful, and economical outcomes. Here are some crucial tactics to think about:
Manufacturability-focused design (DFM):
- Know Your Machine Capabilities:
Become acquainted with the resources available to the CNC machine shop you will be collaborating with. This covers elements such as minimum feature sizes, accessible tool types, and maximum material size. Create your prototype with these limitations in mind for effective machining.
- Reduce Complexity:
Although CNC machining is capable of handling complex designs, it is usually faster and less expensive to build simpler prototypes. Aim for a balance between manufacturability and usefulness.
- Wall Thickness:
Throughout your design, keep the wall thickness constant and adequate. Overly thin walls can make a part brittle to manufacture. Think about the minimum wall thicknesses that are advised depending on the selected material.
- Attributes and Limitations:
On your design, be sure to provide explicit tolerances for all important dimensions. Avoid extremely tight tolerances, though, as these can greatly raise the cost and duration of machining.
- Chamfer and Fillet:
Edges are prone to stress concentrations and might be difficult to machine. To increase strength and facilitate machining, add fillets and chamfers.
Design for Functionality:
- Assembly and Disassembly:
Take into account the methods for assembling and disassembling any multiple-part prototype. Slots, tabs, and threaded inserts are examples of design elements that make assembling simple.
- Functionality Testing:
Verify that the elements required for the targeted functionality testing are included in your design. If necessary, take into account access points for test apparatus or sensors.
Design for Cost-Effectiveness:
- Nesting:
Consider nesting similar elements on the material sheet when creating numerous of them. This lowers expenses by maximizing material utilization and minimizing waste.
- Finishing Design:
Think about how the ultimate surface finish will be obtained. A rougher surface may be left by some machining procedures than by others. If more finishing procedures are required, make plans for them.
Conclusion:
It is a powerful tool that empowers businesses to bridge the gap between design and reality. It offers unmatched precision, versatility in material selection, and the ability to create functional and visually appealing prototypes. Contact HuaYu Prototype today to discuss your prototype CNC machining needs and get a free quote!