The Comprehensive Guide to CNC Machining Industries
The Power of Precision: A Guide to CNC Machining Industries
The creation of intricate and accurate parts has been revolutionised by computer numerical control (CNC) machining, which has completely changed modern manufacturing. This article explores the world of CNC machining industries, looking at its many uses, advantages, and range of services.
Understanding of CNC Machining
CNC machining is fundamentally a subtractive manufacturing technique. A machine tool is operated by a computer program that carefully directs cutting instruments to remove material from a workpiece and shape it into the desired final form. Since it enables the construction of complex designs and strict tolerances, CNC machining is an essential component of contemporary manufacturing.
The Diverse Landscape of CNC Machining Industries
Because of its adaptability, CNC machining is used in many different sectors, each with its own set of needs and uses. Here is a brief overview of some of the CNC machining industries that use CNC machining to their advantage:
- Aerospace:
This sector of the economy requires lightweight, highly durable parts that are resistant to harsh environments. These parts are expertly crafted by CNC machining from materials like titanium and aluminium, guaranteeing the effectiveness and safety of aircraft.
- Automobiles:
A wide range of components, including delicate engine parts and sophisticated suspension systems, are machined using computer numerical control (CNC) technology. Modern automobiles depend heavily on CNC machining’s ability to make parts with high precision and consistent quality for safe and efficient operation.
- Medical Devices:
Exceptionally precise and sterile parts are needed in the medical profession. By producing intricate medical devices and implants, CNC machining satisfies these requirements and advances healthcare.
- Oil & Gas:
Robust and dependable components are essential due to the severe conditions that the oil and gas sector faces. Oil and gas extraction procedures run well because CNC machining produces components that can endure high pressure and harsh temperatures.
- Electronics:
The drive towards miniaturisation in electronics greatly depends on the production of complex circuit boards and other electronic components using CNC machining. The accuracy of CNC machining guarantees that these parts operate well in small electrical devices.
- Mould Making:
The creation of moulds for many production processes is a crucial function of CNC machining. Because of the great accuracy of CNC machining, precise and long-lasting moulds are created, resulting in the reliable manufacturing of high-quality parts.
- Rapid Prototyping:
In the process of developing a new product, rapid prototyping is essential. Prototypes may be quickly created with CNC machining, allowing engineers and designers to test and improve their concepts before going into mass production.
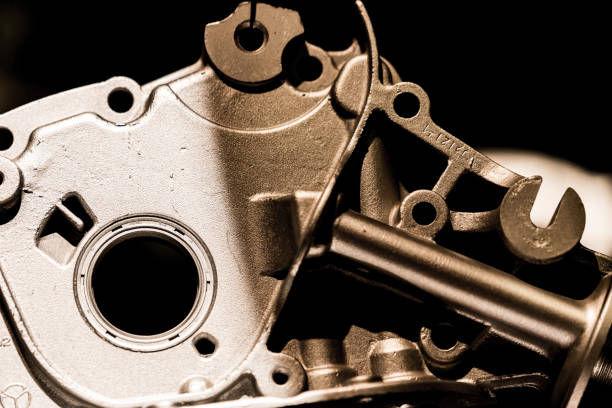
Beyond Sectors: An Overview of CNC Machining Offerings
The field of CNC machining offers a wide range of services to meet various production requirements. Some of the most in-demand CNC machining services are listed below:
- CNC Machining Services:
The general milling of different materials with CNC machines is referred to as CNC machining services. We provide customers with full CNC machining services, guaranteeing premium products for their particular requirements.
- Precision machining:
The production of products with extremely tight tolerances and great accuracy is the focus of precision machining. Precision machining jobs are best suited for CNC machining, which produces parts that satisfy the strictest requirements.
- CNC Parts Manufacturing:
This service entails employing CNC machining throughout the whole component production process. Customers may get a one-stop shop for CNC parts manufacture, which includes everything from design support to material selection and final machining.
- CNC Prototyping:
This technique uses CNC machining to swiftly and effectively build prototypes. Faster product development cycles and design iterations are made possible by this.
What are the basic functions of CNC machining?
- Contract Manufacturing:
In contract manufacturing, a specialised manufacturer is hired to produce parts or components. Numerous CNC machine shops give their clients access to their knowledge and resources through contract manufacturing services.
- 5-Axis Machining:
This sophisticated CNC machining method makes use of equipment with five axes of motion, allowing for the production of extremely detailed objects with complicated geometries.
- CNC Milling:
CNC milling is the process of removing material from a workpiece using rotary cutting tools to create a variety of forms and features.
- CNC turning:
CNC turning is the process of shaping cylindrical workpieces using rotating cutting tools to create parts like shafts and gears.
- Machining Services:
This broad phrase includes both conventional techniques like manual machining and more recent ones like CNC machining.
- Custom Machining:
This type of machining is used to create items according to the precise specifications and designs of customers. Because of its versatility, CNC machining industries are perfect for customised tasks.
The Strength, Accuracy, and Efficiency of CNC Machining
With good reason, CNC machining has emerged as a key component of contemporary production. Traditional techniques just cannot equal the special combination of power, accuracy, and efficiency that this technology delivers. Let’s examine the main benefits that contribute to CNC machining industries high value:
- Unmatched Precision:
The ability to create products with extremely tight tolerances is a strength of CNC machining. Because the process is computer-controlled, human error is eliminated, producing consistently correct components every time. For sectors like aircraft and medical equipment, where even little variations can have serious repercussions, this accuracy is essential.
- Repeatability and Consistency:
A CNC programme may be perfectly repeated once it is set, guaranteeing constant component quality across the course of manufacturing runs. Compared to manual machining, where irregularities are more common, this provides a significant benefit. Reliable final products and more efficient assembly procedures are the results of consistent components.
- Versatility Across Materials:
From soft polymers to tough steel, CNC machines are capable of handling a broad variety of materials. Because of its adaptability, producers may maximise performance and durability by selecting the best material for a given application.
What are the benefits of CNC machining?
- Complexities Simplified:
CNC machining easily handles complex shapes. Previously unthinkable using conventional techniques, five-axis machining centres are capable of producing items with extremely complex forms and features. This creates opportunities for cutting-edge functionality and creative product design.
- Enhanced Productivity:
Numerous operations are automated by CNC machining, which streamlines the manufacturing process and drastically cuts down on production times. This results in more profitable projects that are completed more quickly and more effectively in response to market needs.
- Decreased Waste:
Compared to manual machining methods, CNC machining minimises waste by enabling exact material removal. This lowers expenses and conforms to production methods that respect the environment.
- Enhanced Safety:
By minimising operator participation in the milling process, CNC machines lower the possibility of accidents occurring at work. This promotes a more secure work environment and increases worker safety.
The Magic Behind the Machine: How CNC Machining Works
A cornerstone of contemporary production, CNC machining turns a raw material block into an exact and complex item. However, how precisely does this magic occur? Let’s dissect the fundamental procedures of CNC machining:
- Digital Design:
A digital representation of the required portion is used to start the trip. Typically, engineers use Computer-Aided Design (CAD) software to produce this design, carefully defining the geometry, dimensions, and tolerances of the item.
- Programming the Machine:
The CNC machine is then given precise instructions on how to move its cutting tools using a CNC program, which is created from the CAD design. The toolpath, feed rates, spindle speeds, and other crucial variables for machining the item are specified in this program.
- Machine Setup:
The CNC machine is ready for the job with the programme in hand. The machine’s worktable is firmly clamped down on the selected raw material. The material to be machined and the required characteristics are taken into consideration while choosing cutting tools.
- Subtractive Manufacturing:
This is where the action happens. The CNC device is the focal point. The computer control system of the machine finely controls the cutting instruments using preprogrammed instructions. By gradually removing material from the workpiece, these tools shape it into the final shape required by the computer design.
Performance of CNC machining:
- Precision and Control:
The ability of CNC technology to provide exact control is what makes it magical. The computer keeps an eye on the cutting instruments’ location and motion to make sure they follow the preprogrammed route precisely. It is possible to create items with precise features and tight tolerances with this degree of control.
- Many Axes of Movement:
Contemporary CNC machines are equipped with three, four, or five axes, however, this is not always the case. This makes it possible for the cutting tool to move in several directions at once and machine intricate forms from every aspect.
- Efficiency and Automation:
CNC machining is a very automated operation. The machining process may be carried out with little assistance from humans after the programme is configured and the machine is ready. Increased productivity, quicker production schedules, and consistent part quality are all results of this automation.
Conclusion:
HuaYu Prototype, CNC machining industries, is skilled in taking your product concepts from early prototypes to mass manufacturing. Our team of professionals, equipped with cutting-edge technology, is skilled in handling complex designs and exacting aesthetic requirements. To meet a range of needs, we provide a comprehensive range of on-demand manufacturing services.