The Essential Guide to CNC Machining Processes: Everything You Need to Know
The Complete Manual for CNC Machining Processes: Idea to Production
Workstation Manufacturing has undergone a revolution because to numerical control (CNC) machining, which has changed how we make intricate and accurate parts. This article explores the world of CNC machining processes and acts as your one-stop resource. We’ll look at how it functions, the various varieties that are available, its benefits and drawbacks, and the wide range of materials that it can handle. We’ll also discuss the advantages of rapid prototyping, contrast CNC machining with conventional techniques, and clarify the variables affecting tolerance and cost.
Demystifying CNC Machining: How Does it Work?
Picture a master sculptor painstakingly crafting a masterpiece out of a block of stone. Now swap out the chisel with a high-speed cutting instrument and the sculptor for a computer program. That is what CNC machining is all about. In this subtractive manufacturing method, a machine is operated by a computer to remove material from a solid workpiece in order to mold it into the desired final form.
Below is a summary of the essential steps:
- Design and programming:
Engineers utilize Computer-Aided Design (CAD) software to generate a digital three-dimensional model of the component.
- Toolpath Generation:
A set of instructions (G-code) that specify how the cutting tool will travel along different axes is created from the CAD model using specialized software.
- CNC Machine Setup:
The machine table is secured with the selected workpiece material. Choosing the right cutting tools depends on the material and desired finish.
- Machining Process:
Using the G-code software as a guide, the CNC machine carefully eliminates material to realize the design.
- Final Touches:
The machined part may go through extra finishing procedures like polishing or anodizing, depending on the application.
A Spectrum of Capabilities: Unveiling the Types of CNC Machining Processes
There is no one-size-fits-all approach to CNC machining. This adaptable technology provides a variety of processes, each with unique advantages and uses. Knowing these procedures gives you the ability to select the appropriate instrument for the task.
- CNC Milling:
The mainstay of CNC machining, milling involves shaping complex geometries on a workpiece with the use of spinning cutting tools. Imagine a high-speed carving tool that follows an exact route and removes material in several directions to form intricate forms, slots, and pockets. Because of its versatility, milling is perfect for a variety of items and businesses.
- CNC Turning:
CNC turning is the only option for crafting magnificent circular items. While a fixed cutting tool carefully eliminates material to obtain specified diameters and lengths, the workpiece rotates in a manner similar to that of a potter’s wheel. Consider creating the ideal chess piece. CNC turning is a mainstay in the production of shafts, gears, and other rotationally symmetrical parts since it excels at such tasks.
- CNC Drilling:
Need exact holes drilled? Try CNC drilling. The solution is provided by CNC drilling. Using specialized drill bits, this method makes holes in your workpiece that are precisely the right size and location. Consider installing electronic components or constructing elaborate furniture. CNC drilling guarantees precise and consistent hole production, reducing errors and saving time.
Weighing the Benefits of CNC Machining Methods: An Achievement in Accuracy and Effectiveness
Manufacturing has been completely transformed by CNC machining, and for good cause. This technology is superior than conventional approaches due to its many benefits. Let’s examine the main advantages that make CNC machining an appealing option for producers in many sectors.
- Unmatched Repeatability and Precision:
CNC machines are the pinnacle of precision. The cutting tool is moved consistently and precisely by computer control, producing pieces that exactly fit the digital design. This changes the game for applications demanding tight tolerances by removing human error and guaranteeing consistent quality throughout manufacturing cycles.
- Flexibility in Design Unleashed:
The limitations of conventional techniques are lifted off designers thanks to CNC machining. Difficult shapes, fine details, and complex geometries are all attainable. The production of highly functional components and inventive product development are made possible by the capacity to convert complex CAD concepts into tangible pieces.
- Automation at its Best:
The days of painstaking manual machining are long gone. CNC machines follow preprogrammed instructions to function independently. Over time, this automation increases efficiency and cost-effectiveness by minimizing human error, increasing manufacturing speed, and reducing reliance on skilled labor.
- Material Flexibility:
A Bridge for Various Needs Certain materials can be machined using CNC technology. A wide range of materials may be accurately machined, including lightweight polymers, wood, and strong metals like titanium and steel. Because of its adaptability, producers can select the best material for their purpose, guaranteeing top functionality and performance.
- Scalability for Every Project:
CNC machining easily adjusts to your needs, whether they are for a single prototype or a high-volume production run. CNC machining is appropriate for both high-volume manufacturing requirements and low-volume prototyping due to its capacity to scale production in response to demand.
Building Blocks of Success: Materials Used in CNC Machining
The versatility of CNC machining processes is demonstrated by its capacity to process a wide range of materials, each of which has distinct qualities that affect the finished result. Gaining knowledge about these resources enables you to decide on your project wisely and produce the best outcomes.
Metals: The Foundation of a Lot of Industries
- Aluminum:
Aluminum is a common material for applications needing strength-to-weight ratio, such as electronic enclosures and aircraft parts. It is lightweight, corrosion-resistant, and easily machinable.
- Steel:
A cornerstone in many sectors, steel offers remarkable strength and endurance. Steel’s various grades meet a variety of applications, from construction equipment to automotive parts like gears and shafts.
- Stainless Steel:
This material combines strength and resistance to corrosion, making it perfect for parts that need to be hygienic or exposed to severe environments. Consider devices used in the medical field, food processing industries, and maritime settings.
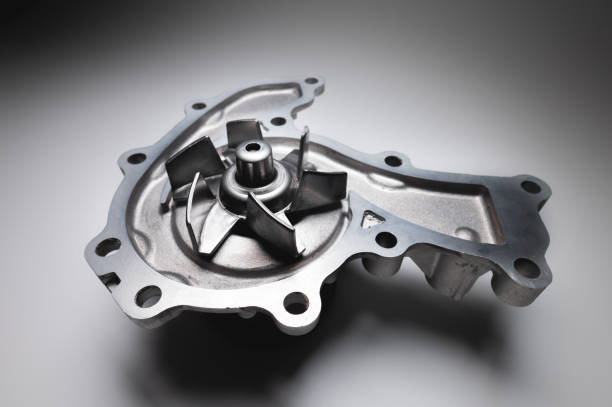
Beyond Metals: Broadening the View
- Plastics:
Available in a range of formulations with distinct qualities, plastics provide a lightweight substitute for metals. Toys and electronic housings are made of ABS, which is renowned for its strength and resilience to impact. High-performance plastics like Delrin® work well in applications like gears and bearings where dimensional stability and wear resistance are essential.
- Wood:
CNC machining revitalizes the woodworking industry. Different kinds of wood can be expertly used to create intricate furniture parts, decorative accents, and even unique architectural items.
- Composites:
Materials with outstanding strength-to-weight ratios, such as carbon fiber and fiberglass composites, are well suited for demanding applications. Consider durable yet lightweight industrial items, athletic goods, and high-performance aerospace components.
A Vast Range of Uses: Where CNC Machining’s Imprint Is Found
The applications of CNC machining are not limited to just one industry; they are widely spread and influence the items we use on a daily basis. Let’s examine a few well-known uses for CNC machining that are essential to understanding:
- Aerospace:
In the aerospace sector, accuracy and dependability are crucial. CNC machining meets both needs by producing vital parts for satellites, spacecraft, and aircraft. Modern aircraft depends on CNC machining for everything from complex wing components to lightweight, strong engine parts.
- Automotive:
Consistency and efficiency are key factors in the automotive industry’s success. Production is streamlined using CNC machining, which produces parts of superior quality for a range of uses. Consider engine blocks, complex transmission gears, and even specially designed body parts. CNC machining ensures accuracy and consistency, which keeps cars operating properly.
Accurate and dependable equipment is essential to the medical industry. CNC machining rises to the occasion by producing essential implants and medical equipment. For the best possible patient care, surgical tools, prosthetics, and even little parts of medical equipment are all painstakingly machined to ensure precision and functionality.
- Consumer Electronics:
CNC machining is essential to the smooth, high-tech devices we use every day. From the complex casings of laptops and smartphones to the minuscule parts that reside inside of them, CNC machining guarantees accurate measurements and uniform quality, providing the dependable performance we anticipate from our daily gadgets.
Beyond the Well-Known Names: Unexpected Uses
The influence of CNC machining goes beyond these well-known sectors. It is essential to the creation of:
- Custom components for product development and prototype
- Dies and molds for different manufacturing procedures
- Both ornamental and architectural elements
- Displays and signs for branding and advertising
- High-performance athletic supplies and gear
A Cosmic Web of Opportunities:
This is by no means an exhaustive list of the many uses for CNC machining. Because of its adaptability, it may serve a broad range of purposes and is an invaluable tool for numerous enterprises and sectors. The advantages of quick prototype using CNC machining and cost-influencing aspects will be discussed in more detail in the following section.
Conclusion:
HuaYu prototype has millions of pieces spanning a wide range of prototype experience. We take great pride in being a reliable partner to the transportation, medical, AI, and industrial machinery sectors. Our expertise in CNC machining processes goes far beyond small-scale components at Huayu. For large-scale components made of metal or plastic, we specialize in both production runs and prototyping.