Title: Low Volume CNC Production: Cost-Effective Solutions for Your Needs
Unleashing Potential: A Comprehensive Guide to Low-Volume CNC Production
The capacity to make high-quality components in small numbers is more important than ever in the dynamic industrial environment of today. This is where low-volume CNC production shines, changing the game for companies of all kinds with its unmatched efficiency and flexibility. Low-volume CNC machining enables you to close the gap between prototype and mass production, regardless of whether you’re an established business looking for an affordable solution for custom components or a startup bringing your original concept to reality.
What is Low-Volume CNC Production?
It produces bespoke components in tiny quantities, usually a few hundred to a single piece, by using Computer Numerical Control (CNC) machining technology. Through the use of digital design files (CAD), computer-guided tools are precisely controlled in this process, turning solid materials into complicated and useful components.
Benefits of Low-Volume CNC Production:
- Fast Design Iteration and Prototyping:
Before committing to bigger production runs, CNC machining enables the speedy manufacture of working prototypes, allowing for quick testing and design refinement. This capacity to prototype quickly cuts down on the time and expense of development compared to more conventional approaches.
- Cost-Effectiveness for Short Runs:
It reduces the requirement for costly tooling as compared to conventional production techniques like injection moulding or casting. This makes it an extremely economical choice for manufacturing runs with limited quantities, particularly for complicated geometries that could need specialised tools in other techniques.
- High-quality, Accurate Parts:
CNC machining offers remarkable repeatability and precision, guaranteeing constant surface finishes and dimensional correctness for every component in your small-batch manufacturing process. This results in components that perfectly operate within your application and satisfy your exacting criteria.
- Flexibility in Material Selection:
CNC technology allows for the machining of a large variety of materials, including composites, metals, polymers, and wood. Because of its adaptability, you may choose the material whose strength, weight, and usefulness best suit the needs of your project.
- On-Demand Manufacturing:
Low-volume CNC production provides the flexibility to produce components as needed, removing the requirement for significant upfront inventory commitments. Businesses bringing new items to market or those with varying manufacturing demands may find this very helpful.
Applications of Low-Volume CNC Production:
Low-volume CNC manufacturing has a wide range of applications in several sectors.
- Prototyping & Product Development:
CNC machining is essential for producing working prototypes for testing and design iterations in a variety of industries, including consumer electronics and medical equipment.
- Bespoke Parts & Components:
It makes it possible to create bespoke parts that are exactly suited to your needs, whether they are replacement parts for outdated equipment or specialised components for particular applications.
- Aerospace and Defence:
High-precision, dependable parts are required to meet the stringent standards of these industries. Complex components such as aeronautical instruments and engine parts can be produced using low-volume CNC machining.
- Automobile Manufacturing:
It is essential to the automotive sector since it is used to create anything from unique automobile prototypes to specialised parts for race cars.
- Medical Devices and Implants:
It is perfect for producing medical devices and implants that adhere to strict medical requirements because of its precision machining capabilities and biocompatible materials.
Selecting the Perfect Partner: Your Guide to Low-Volume CNC Machining Success
It is a potent way to produce small quantities of high-quality components. The success of your project, however, depends on choosing the right CNC machining partner. This is a thorough approach to determining the best fit:
- Experience and Expertise:
Give top priority to a partner with a track record of success in low-volume machining, especially in your sector and using the materials of your choice. Seek out a business that exhibits a thorough comprehension of the precise material qualities pertinent to your project, as well as the machining process itself. Their technical expertise guarantees a smooth conversion of your idea into a high-calibre, working prototype or component.
- Ability Complement
To be sure your partner can manage the complexity of your design, evaluate their machining skills. Take into account the number of axes (3, 4, or 5-axis) on their CNC machines as well as their familiarity with the material (metal, plastic, etc.) that you have selected. Optimising outcomes is ensured by matching skills to project requirements. For example, complex geometries can be needed for a 5-axis machining partner.
- Interaction and Cooperation
Communication that works is essential to the project’s success. To turn your idea into a reality, pick a partner who actively listens to your needs, gives transparent progress reports, and encourages teamwork. Choose a business that encourages candid conversation and collaborates to improve your design for effective machining.
Things to know before selecting a reliable partner:
- Efficiency of Turnaround Time
Talk to possible partners about the turnaround time you’d want to achieve. A trustworthy partner will be able to fulfil your deadlines without sacrificing quality standards. Realistic expectations for project completion are ensured by having an understanding of their workload.
- Ensure Quality
Find out about the partner’s methods for quality control. Reputable businesses will ensure surface finish, dimensional correctness, and compliance with your standards with a strong quality assurance system. This guarantees that the parts you receive fulfil your functional requirements and are of consistently high quality.
Bridging the Gap: How It Streamlines Your Journey from Prototype to Production
It might be difficult to get from a creative concept to a large-scale manufacturing run. Early-stage research is severely hampered by the high minimum order numbers and costly tooling associated with traditional production techniques. This is where mass production and prototypes can be bridged more affordably and effectively using low-volume CNC machining, which changes everything.
The bottleneck in prototypes:
To provide critical testing and design iterations, prototyping is a critical step in the product development process. Nevertheless, conventional prototype techniques, such as 3D printing, may have drawbacks. There might be problems later in the production process if the material’s functionality or qualities don’t match the finished product.
Low-Volume CNC Comes to the Aid:
It provides a potent remedy. Using the same materials you want to use for mass production, this method accurately produces functioning prototypes through the use of computer-controlled equipment. This offers several significant benefits:
- Realistic Testing:
CNC-machined prototypes faithfully replicate the material characteristics and functionalities of the finished product. This makes it possible to thoroughly test and find any possible design problems before starting large-scale manufacturing.
- Rapid Design Iteration:
Quick design modifications and the creation of updated prototypes are made possible by the speed and adaptability of CNC machining. Comparing this iterative procedure to previous methods, development time and expenses are dramatically reduced.
- Smoother Transition to Mass Production:
The process of moving from low-volume CNC to mass production is made easier by having already established the machining process and the compatibility of the material. This reduces the possibility of delays and guarantees a seamless ramp-up for large-scale production.
Past Prototyping:
Not only is low-volume CNC production useful for prototyping. Additionally, this technology may be used for:
- Short-Run Manufacturing:
Do you require a small quantity of parts for a market test or a new product launch? When compared to conventional processes, low-volume CNC manufacturing is a more economical option.
- Custom Parts & Components:
CNC machining makes it possible to create distinctive and customised parts, which are perfect in circumstances when mass manufacturing isn’t practical.
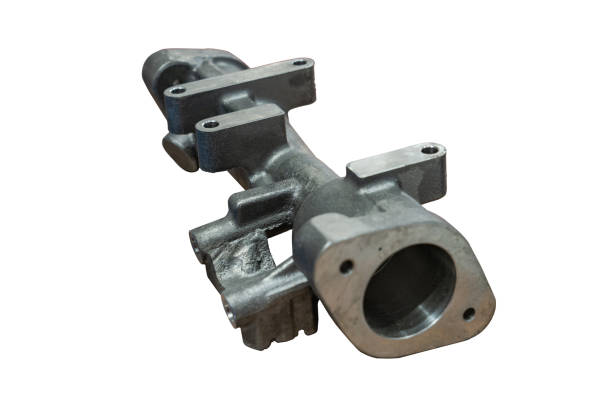
Why low volume CNC production is Cost-effective solution for projects?
The changing industrial landscape of today keeps cost-effectiveness at the forefront of concerns. Traditional manufacturing techniques can frequently be a budgetary barrier for projects needing small-batch production runs. This is where low-volume CNC manufacturing comes into play, providing a strong answer with notable financial advantages.
- Eliminating Expensive Tooling:
Specialised tooling is essential to traditional manufacturing methods like die casting and injection moulding. The cost of designing and producing these tools may be very high, particularly for intricate geometries. This upfront expense is eliminated with low-volume CNC manufacturing. CNC machines eliminate the need for specialized tools for each project by controlling the milling process with digital design files (CAD). This results in considerable cost savings—especially for small-scale production operations.
- Maximining the Use of Materials:
CNC machining is known for its remarkable accuracy and little material waste. CNC machines, in contrast to certain subtractive manufacturing techniques, only remove material that is required to obtain the desired final form. This lowers overall material consumption and minimizes waste, which saves money—especially when working with pricey materials.
Importance:
- Allowance for Modifications in Design:
For traditional methods to adapt to changes in design, a substantial investment and effort are frequently needed. CNC manufacturing at low volumes provides more flexibility. Changes to the digital design file and a new run of the CNC programme enable fast and economical design revisions because tooling is not required. Over time, this iterative method saves you money by reducing material waste and production runs of obsolete prototypes.
- Economical Prototyping:
Comprehensive testing and design iterations are necessary for producing a successful product. Even though 3D printing is a useful technique for prototyping, the material qualities of the finished object might not always be precisely represented. It enables you to use the same materials you intend to use for mass production to produce working prototypes. This makes testing more realistic and lowers the possibility that expensive design problems will be found later.
Conclusion:
An ideal low-volume CNC production partner, HuaYu, is an invaluable addition to your product development process by carefully weighing these considerations. Your idea may become a high-calibre prototype or small-scale production run with the correct partner at your side, opening the door for a fruitful product launch. Please get in touch with HuaYu Prototype to explore your needs for low-volume CNC machining; we would be delighted to work with you!