Unlock Precision & Efficiency: CNC Machining Capability at HuaYu Prototype
The Power of Precision: Unveiling the Capability of CNC Machining
Manufacturing has been transformed by computer numerical control (CNC) machining. With the use of this revolutionary technology, intricate and highly accurate parts may be produced via a computer-controlled process. Understanding CNC machining capability is crucial for companies looking to get dependable, high-quality products. This thorough introduction explores the many functions, industrial uses, and advantages of CNC machining, delving deeply into the subject.
Demystifying CNC Machining: Capabilities and Processes
Fundamentally, CNC machining is the use of computer software to operate machinery. This program converts a digital design—typically produced using CAD, or computer-aided design—into a set of commands for the machine, directing it through the exact motions needed to produce the desired item. The CNC machining capability to deal with a wide range of materials, including plastics, wood, and metals like steel and aluminum, accounts for its flexibility. A closer look at a few essential CNC machining features is provided below:
- High-precision CNC machining:
CNC devices are incredibly accurate and can produce items with micron-scale tolerances. Because of this, they are perfect for uses demanding a high degree of accuracy, such as those in the aerospace and medical device sectors.
- Multi-axis CNC machining:
With the ability to have three, four, or five axes, modern CNC machines can manufacture complicated geometries with only one setup. This saves a great deal of manufacturing time by doing away with the requirement for several machining procedures.
- Complex CNC machining:
One of CNC machining’s main characteristics is its capacity to handle complex designs. CNC machines can precisely handle even the most difficult designs, from complex gears and molds to bespoke components with distinctive characteristics.
- Large-scale CNC machining:
CNC machines are available in a range of sizes to accommodate projects of all shapes and sizes. Massive workpieces may be handled by large-scale CNC machines, which makes them appropriate for heavy equipment manufacture and shipbuilding.
Additional consideration:
- CNC machining for small batches:
CNC machining’s versatility makes it possible to produce small quantities quickly and effectively. This is especially helpful for low-volume manufacturing runs, bespoke parts, and prototyping.
- Quick prototyping:
One major benefit of CNC machining is its ability to swiftly generate prototypes from a digital design. Faster product development cycles and design iterations are made possible by this.
- CNC machining with tight tolerances:
As previously stated, CNC machining is particularly good at creating components with extremely tight tolerances. This guarantees that all of the parts in an assembly fit well and are of constant quality.
Unveiling the Applications: Industries that Leverage CNC Machining:
Numerous sectors are among the many that CNC machining has applications in. Here are a few well-known instances:
- Aerospace:
To create high-precision parts like landing gear, engine components, and aircraft parts, the aerospace sector mostly relies on CNC machining.
- Medical device:
Because medical equipment frequently needs to be manufactured with precise dimensions and complex designs, CNC machining is a great fit for producing implants, prosthetic limbs, and surgical tools.
- Automobile:
CNC machining is essential to the automobile sector since it is used in everything from engine blocks and transmission components to vehicle bodywork and speciality pieces.
- Mold making:
One of the main uses of CNC machining in the manufacturing industry is the creation of intricate molds for a variety of applications, including injection molding and blow molding.
- Military:
CNC machining is used in the defence sector to produce gun parts, weapon components, and other essential military gear.
- Electronics:
Detailed electronic components like circuit boards, heat sinks, and enclosures are made possible thanks in large part to CNC machining.
- Consumer products:
CNC machining helps produce a wide range of consumer goods, including toys, electronics, sporting goods, and home appliances.
The Allure of Efficiency: Benefits of Utilizing CNC Machining:
There are many more benefits to using CNC machining in your production process than merely producing accurate products. Here are just a few of the many advantages that manufacturers find attractive when considering CNC machining:
- Cost-Effectiveness:
The long-term cost reductions from CNC machines are indisputable, despite the machine’s initial large investment. By using computer-controlled procedures and optimal cutting routes, CNC machining decreases material waste and lowers human error. Comparing this to more conventional production techniques, substantial cost savings result. Furthermore, the capacity to create parts in tiny quantities removes the requirement for costly inventory control.
- Quick Turnaround:
When compared to conventional techniques, CNC machining capability offers remarkable speed and efficiency. Faster turnaround times are made possible by the process’s automation, which drastically cuts down on manufacturing time. This is especially helpful for projects with short deadlines and prototyping when quick design iterations are essential.
- Dependable and Consistent Quality:
CNC machining guarantees consistent and dependable part quality by eliminating human error from the process. A digital design is used to create precise replicas of every element, ensuring flawless consistency across a production run. Applications needing exact assembly and functionality depend on this consistency.
- Flexibility and Scalability:
CNC machining can handle a wide range of project sizes. CNC machines can be used for small-batch bespoke part manufacture, large-scale production runs, or a single prototype. Businesses may increase their production capacity thanks to this scalability without having to make large investments in new gear.
- Lower Labor Costs:
By automating a large amount of the production process, CNC machining lowers the need for manual labor. Lower labor expenses result from this, and competent people can concentrate on other important production-related duties.
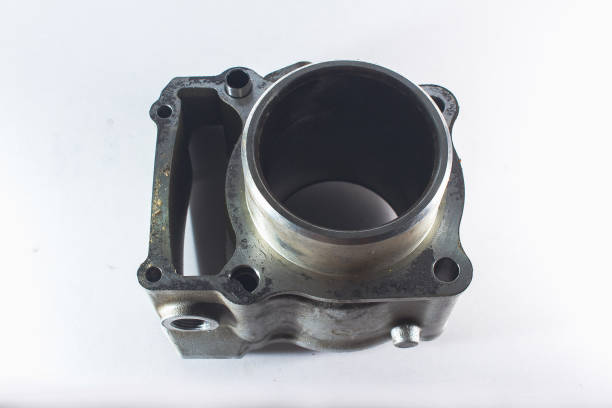
What materials can be CNC machined?
Regarding suitable materials, CNC machining offers remarkable variety. Below is a summary of some of the materials that are most frequently used in CNC machining:
- Metals
Because of its outstanding strength-to-weight ratio, superior machinability, and lightweight nature, aluminum is a preferred choice. It is frequently employed in consumer products, automotive, and aerospace applications.
- Steel:
Comes in a variety of grades and has several qualities, including machinability, strength, and resistance to corrosion. They are extensively employed in industrial, mechanical, and construction applications.
- Stainless steel:
It is well-known for its exceptional resistance to corrosion, which makes it perfect for use in hygienic conditions or challenging settings. utilized in naval components, food processing machinery, and medical devices.
- Titanium:
A very biocompatible, light-weight metal with great strength. utilized in high-performance equipment, medical implants, and aerospace components.
Factors to Consider When Choosing a Material:
The best material for your CNC machining job will rely on several variables, such as:
- Part Function:
Take into account the part’s function as well as the pressures it will experience.
- Material Properties:
Consider the material’s weight, strength, resistance to corrosion, and other pertinent characteristics.
- Machinability:
The cost and duration of production are affected by the ease of machining of certain materials over others.
- Cost:
The total project budgeting process takes material costs into account. Speak with an experienced CNC machining service provider for comprehensive advice and suggestions on material selection for your unique CNC machining requirements.
The Rapid Prototyping Process with CNC Machining:
- Design Creation:
To begin, a 3D CAD model of the intended prototype must be made. The machining instructions for the CNC will be generated using this model.
- Material Selection:
It’s important to pick the right material for the prototype. Cost, practicality, and aesthetics are a few examples of factors to take into account. CAM programming involves translating the CAD model into a CNC program, or set of instructions, that the CNC machine can comprehend. The toolpaths and motions needed to build the component are described in detail by this software.
- CNC Machining:
To construct the actual prototype, the CNC machine accurately removes material from the selected workpiece while carrying out the program.
- Evaluation and Iteration:
Next, the functionality, fit, and shape of the prototype are assessed. This input is utilized to improve the design and create new iterations as needed.
CNC Machining and Finishing: A Perfect Match for Flawless Parts
Precision is one area where CNC machining shines, but the process doesn’t stop there. CNC machining is frequently combined with several finishing methods to produce a product that is completed. This combination of methods guarantees that the components have the appropriate functional and aesthetic surface quality in addition to meeting dimensional criteria. Here’s an example of how CNC machining and finishing work well together:
- Surface smoothing:
Surface machining using CNC technology may result in minute tool markings. Finishing methods such as polishing, bead blasting, or sanding remove these flaws to provide a smooth, visually appealing surface.
- Functional Enhancement:
A part’s functionality can be enhanced by certain finishing techniques. Anodizing metal, for instance, produces an oxide layer that is resistant to corrosion, while powder coating provides a long-lasting and colourful finish
- Dimensional Accuracy Tuning:
The CNC machining capability is quite accurate, other finishing methods, such as honing or lapping, can further fine-tune dimensional tolerances to provide a surface profile that is extremely precise and smooth.
Conclusion:
We at HuaYu Prototype make use of CNC machining’s full capability. We smoothly incorporate this technology into your project’s process to guarantee a seamless shift from low-volume manufacturing to prototype creation. Our dedication to accuracy and quality ensures reliable outcomes while reducing process interruptions.