Unmatched Precision: CNC Machining Copper Parts for Demanding Applications
Unlocking Copper’s Potential: An Overview of Ultra-Accurate CNC Machining
Many contemporary uses depend on copper, the reddish-brown metal valued for its remarkable electrical and thermal conductivity. Engineers and designers in a variety of industries choose copper because of its special qualities, which make it suitable for everything from complex electronics components to effective heat sinks. However, how do you accomplish the exact forms and features needed for these parts? Let me introduce you to CNC machining, a computer-controlled subtractive manufacturing technique that turns copper into extremely personalized pieces.
This thorough manual delves deeply into the field of CNC machining copper, examining its benefits, procedures, uses, and issues. This post gives you the tools to make use of the potential of CNC machined copper for your upcoming project, regardless of your level of experience as an engineer or where you are in your research of metal fabrication.
Why Choose CNC Machining for Copper?
When it comes to forming copper into the desired shape, CNC machining copper provides several strong benefits. The following are some main advantages:
- High Precision:
By using computer-controlled cutting tools, CNC machines can produce very precise and repeatable results, even for the most complex designs. CNC machining makes it possible to achieve complicated geometries and tight tolerances, which makes it perfect for demanding applications.
- Superior Surface Finishes:
Machined copper items can have smooth, consistent surface finishes thanks to the exact control of CNC machining. Time and resources are saved since fewer post-processing processes are required as a result.
- Versatility:
A variety of copper alloys, each with unique qualities, can be machined using CNC technology. Because of its adaptability, you can select the ideal material by taking into account characteristics like strength, conductivity, and machinability for your particular application.
- Quick Turnarounds:
Compared to conventional methods, modern CNC machines run at fast speeds, greatly cutting production times. Prototyping and low-volume production runs benefit most from this.
- Expense-effectiveness:
Although there may be a greater setup fee initially, CNC machining provides excellent material use and lower waste. In the long run, cost savings may also result from the process’s speed and efficiency.
Exposing the Copper CNC Machining Process
Copper is machined using a CNC machine in several crucial steps:
- Design and Programming:
To begin, make a 3D computer-aided design, or CAD, model of the copper part you want to create. The machine tools’ movements are then managed by a set of instructions called CNC code, which is created from this digital design.
- Material Selection:
The project’s particular requirements are taken into consideration when selecting the suitable copper alloy. During this selection process, variables including strength, machinability, and electrical conductivity are taken into account.
- Setup of the Machine:
The CNC machine is ready for work. After the copper workpiece is firmly in position, the proper cutting instruments are chosen and loaded.
- Machining:
The CNC code assumes control and directs the cutting instruments to precisely and carefully remove material from the copper workpiece, gradually forming it into the required shape. Various CNC machining processes, such as turning, milling, drilling, and tapping, may be used.
- Inspection and Post-Processing:
Following machining, the completed part is thoroughly inspected to make sure it satisfies the requirements. Additional post-processing operations like as surface finishing or deburring may be needed, depending on the application.
Exposing the Extensive Uses of CNC Machined Copper
Due to its remarkable electrical and thermal conductivity, copper is used in many contemporary marvels. However, how can we accomplish the complex forms and features required for these uses? Let me introduce you to CNC machining, a computer-controlled subtractive manufacturing technique that turns copper into extremely personalized pieces. Copper can be used in so many different ways thanks to CNC machining, which makes it a vital component of many different sectors. Now let’s examine a few well-known uses for CNC-machined copper:
Fuelling the Revolution in Electronics:
The electronics sector uses a lot of copper that has been CNC machined. Because of its excellent conductivity, it’s perfect for:
- Circuit boards:
The building blocks of electrical gadgets, circuit boards frequently have complex copper lines that are extremely precisely carved.
- Heat Sinks:
These essential parts dissipate heat, and the sophisticated copper shapes made possible by CNC machining increase the effectiveness of heat transfer.
- Connectors:
CNC-machined copper connectors provide accurate and long-lasting solutions for dependable connections inside electronic systems.
- Bus Bars:
CNC machining allows for the creation of intricate copper shapes with excellent conductivity, which is advantageous for bus bars, which distribute electrical power throughout a system.
Beyond Technology: A Resource for Various Needs
Beyond electronics, CNC machining copper is used extensively in several other industries. These industries include:
CNC machined copper is biocompatible and conductive, and it is used in electrodes, implants, and surgical equipment.
- Aerospace:
Copper’s weight-to-strength ratio and thermal conductivity make it perfect for use in heat exchangers, electrical cables, and engine parts.
- Automotive:
CNC machined copper maintains automobiles operating well in everything from bus bars to electrical harnesses and radiators.
- Renewable Energy:
Due to its superior conductivity, copper is an essential component of solar panel and wind turbine components.
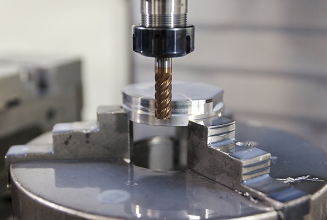
Exposing the Range of Surface Finishes in Copper Machined by CNC
With its varied toolkit and accurate control, CNC machining opens up a range of possible surface treatments for copper components. The functionality you want and the particular program you’re using will determine which finish is best. Now let’s examine the range of surface treatments that can be achieved by CNC cutting copper:
From Rough to Fine: A Range of Choices
As-Machined: This first condition following machining yields a surface that is slightly rough and has obvious tool markings. It might work well for interior components or other applications where surface polish is not a major concern.
- Brushed and machined:
Brushing eliminates tool marks and produces a matte surface with a hint of directional roughness. This finish is more aesthetically pleasing and may be useful in applications where light corrosion protection is required.
- Machined and Bead Blasted:
In contrast to brushing, bead blasting produces a consistent matte finish with a somewhat coarser texture by using tiny abrasive beads. Applications needing better grip or paint adherence can employ this finish, which improves surface adhesion.
- Machined and polished:
This multi-step procedure produces a smooth and glossy finish by gradually removing material and refining the surface. For applications where low friction is essential or where high visual appeal is required, this finish is perfect.
- Electropolishing:
Through the electrochemical process of electropolishing, a minute layer of material is removed, resulting in a surface that is extremely reflective, smooth, and corrosion-resistant. Medical equipment and other applications requiring superior surface quality are better suited for this finish.
Fitting Function to Finish: Making a Sensible Choice
It is necessary to take into account the particular requirements of your application when choosing the best surface finish for your CNC machining copper component. The following are some important things to remember:
- Functionality:
Does the application call for better paint adherence, less friction, or increased corrosion resistance?
- Aesthetics:
Is a more practical matte finish appropriate, or is a glossy, silky surface preferred for visual appeal?
- Expense:
More elaborate finishes like electropolishing often come at a higher expense.
Making the Most of Your CNC-Made Copper Project
You can make wise choices if you know which surface finishes are available and which ones work best for certain applications. When you collaborate with HY Precision a skilled CNC machining service provider, you can take advantage of their knowledge to choose the ideal finish for your CNC machined copper project, guaranteeing both the best results and economical viability.
Unleashing Innovation: Rapid Development with CNC Copper Prototyping
Rapid prototyping, or the ability to quickly bring ideas to life and verify their usefulness, is essential to the world of innovation. CNC copper prototyping has become an effective tool for projects that demand high electrical conductivity and thermal control.
Why Use a CNC to Prototype Copper?
CNC machining is perfect for copper prototypes because it has the following benefits:
- Speed and Efficiency:
CNC machining speeds up the development cycle considerably by enabling the quick fabrication of prototypes in comparison to traditional methods.
- High Precision:
The capacity to create functioning prototypes with precise dimensions and intricate features is made possible by the excellent accuracy and repeatability that come with CNC machining, which is computer-controlled.
- Design Freedom:
The ability to machine complex geometries with CNC technology allows for the production of prototypes that closely mimic the final product design.
- Material Versatility:
You can experiment with different material qualities to maximize the performance of your prototype by using a wide selection of copper alloys that can be used with CNC machining.
Conclusion:
Are you considering how CNC machining copper might be used for your upcoming project? Speak with HuaYu Prototype right now! To make your concept a reality, we provide professional advice and excellent CNC machining services.