What is CNC Machining Aircraft Parts? A Comprehensive Guide
Accurately Piloted: A Handbook for CNC Machining Aircraft Components
The engineering of the aircraft industry is astounding, as each part is essential to maintaining performance, efficiency, and safety. A key technology in this field that makes it possible to create complex and highly precise CNC machining aircraft parts. This thorough introduction explores the world of CNC machining for aeroplane parts, including its benefits, capabilities, and complex processes.
CNC Machining’s Influence on the Manufacturing of Aircraft
By turning computer-aided designs (CAD) into real components, CNC (Computer Numerically Controlled) machining revolutionizes the aircraft manufacturing industry. CNC machines function with remarkable accuracy and reproducibility, as opposed to conventional methods that depend on manual labour, ensuring consistent outcomes that satisfy the exacting requirements of the aerospace sector.
Semantics Based on Entities:
Thanks to this CNC machining aircraft parts, we may now work with a wide variety of materials that are frequently used to create aircraft, such as:
- Aluminium alloys:
Commonly used in aircraft wings and fuselages, aluminium alloys such as 7075-T6 offer an alluring combination of strength, weight reduction, and machinability.
- Titanium alloys:
Notable for their remarkable strength-to-weight ratio and resistance to high temperatures, titanium alloys like Ti-6Al-4V are essential for parts like landing gear that need to be exceptionally strong.
- Inconel alloys:
These nickel-chromium superalloys are perfect for engine parts that are exposed to high temperatures because of their remarkable heat and corrosion resistance.
- Carbon fibre composites:
Carbon fibre composites are being used more and more in aeroplane constructions, especially wings, for applications requiring unparalleled strength and lightweight.
Reaching New Heights: Exposing the Benefits of CNC Machining for Aerospace Components
The aviation industry’s unwavering quest for performance and efficiency depends on precision production. A game-changer, CNC machining aircraft parts has revolutionized the production of complex, high-strength aviation parts. However, what unique benefits can CNC machining provide the aerospace sector? Let us examine the main advantages that are driving this technology to the forefront of aircraft production.
CNC machines ensure outstanding dimensional precision, in contrast to traditional technologies that are prone to human mistakes. The best performance and safety of the aircraft are ensured by the tight tolerances and consistent appearance of each part.
- Overcoming Complex Geometries:
Tooling limitations frequently impede traditional production. These restrictions are lifted by CNC machining, which handles complex designs with ease. This makes it possible to design intricately geometrized, aerodynamically effective components that are essential for contemporary aeroplanes.
- Reducing Weight:
Lightweight design is given priority in modern airplanes to improve fuel efficiency and cargo capacity. Because CNC machining is so good at working with lightweight materials like composites and aluminium, the finished aircraft will weigh less.
- Takeoff for Rapid Prototyping:
CNC machining’s quick turnaround times make it perfect for rapid prototyping. This shortens the development cycle by enabling engineers to test and improve designs quickly before committing to large-scale production.
- Economical for Low-Volume Production:
CNC machining excels at effectively creating small batches. Because of this, it’s the ideal option for producing small quantities of customized aircraft parts or meeting the various demands of the aerospace sector.
CNC machining enables aircraft manufacturers to produce intricate, lightweight, and highly precise parts by utilizing these benefits. Better aircraft performance, shortened development cycles, and eventually a new era of effective and secure air transport are the results of this.
From Sketch to Takeoff: A Detailed Examination of CNC Machining for Aeroplane Parts
An aircraft part’s journey, painstakingly produced with CNC machining, is an intriguing combination of design, precision engineering, and strict quality control. Here’s an overview of the several steps that turn a computer model into an essential part that flies through the air:
- Design and programming:
To produce the needed aeroplane parts, the engineering team painstakingly builds detailed Computer Aided Design (CAD) models. Every dimension and detail is included in this digital blueprint. This CAD model is then converted by specialized software into a CNC program, which is a set of instructions that instruct the machine on how to move and use tools to make the part.
- Material Selection:
The component’s unique function and performance requirements will determine which material is best. High-strength, lightweight materials such as carbon fibre composites, titanium alloys, and aluminium alloys are frequently used in aircraft parts.
- Machine Setup:
To guarantee accuracy, the CNC machine is painstakingly calibrated. The machine is loaded and secured with the selected cutting tools that are appropriate for the chosen material.
- Machining Takes Off:
The CNC machine comes to life as soon as the program is launched. The machine uses a variety of cutting instruments, including drills and milling cutters, to remove material from the solid workpiece and progressively shape it into the desired component while following exact instructions.
- Quality Control is Key:
Strict quality control procedures are followed throughout the process. Dimensional checks guarantee that the component meets all requirements precisely. Techniques such as ultrasonic inspection and X-ray are examples of non-destructive testing (NDT) that are frequently used to find possible internal faults or inconsistencies
Taking Flight Safely: Fulfilling Strict Requirements in Aircraft Part Machining
Safety and painstaking attention to detail are essential in the aviation industry. Every part, from the tiniest rivet to the intricate wing structure, is essential. Even CNC machining aircraft parts CNC machining offers remarkable precision, it must follow a strict set of guidelines and quality requirements to guarantee that these parts are airworthy.
Demanding Rules and Regulatory Organizations:
Government agencies such as the Federal Aviation Administration (FAA) in the United States keep a close check on the aerospace sector. These groups create a thorough set of rules defining the components, production methods, and quality assurance techniques that are required for aviation parts. These rules guarantee the functionality, safety, and structural soundness of every part that is used in flight.
Certifications: A Mark of Excellence
CNC machining firms that specialize in aircraft parts frequently seek certifications such as AS9100 to show their adherence to these rules. A strict Quality Management System designed especially for Aviation, Space, and Defense Organizations is outlined in this globally recognized standard [2]. Comprehensive quality control methods, documented processes, and a constant focus on continuous improvement are required for AS9100 certification.
Unwavering Quality Control Procedures
Adhering to these strict guidelines results in a multi-tiered quality control strategy. Here are a few crucial elements:
- Material Traceability:
The ability to track the origin of each piece of material utilized ensures the integrity of the raw materials used to make airplane parts.
- Dimensional Inspection:
Parts are carefully inspected both during and after the machining process to ensure they match the precise dimensional requirements specified in the design.
- Non-Destructive Testing (NDT):
Methods such as ultrasonic examination or X-rays are used to find any possible interior defects or irregularities in the machined part.
Every aircraft item that comes out of a CNC machine is guaranteed to be accurately built and to fulfil the highest standards of safety and dependability thanks to these strict quality control procedures. Because of this unwavering dedication to quality, CNC machining will be essential to the efficient and safe operation of aircraft in the future.
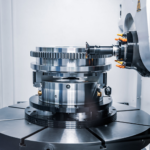
The Future Takes Off: Revealing the Development of CNC Machining in the Production of Aircraft
The aircraft industry’s unwavering quest for efficiency and inventiveness continuously pushes the limits of industrial technology. In the years to come, CNC machining aircraft parts, which is already essential for creating high-precision airplane parts, is expected to undergo considerably more development. Let’s examine some fascinating developments that will influence CNC machining in the production of airplanes in the future:
- Automating and integrating seamlessly:
Automation will grow in the repetitive jobs that human operators currently perform. Automated tool changes, robotic material handling systems, and even integration with other manufacturing processes like surface finishing are all examples of this. Reduced turnaround times, streamlined manufacturing lines, and an all-around more effective workflow were the results.
- The Development of Hybrid Production:
The combination of additive manufacturing (3D printing) and CNC machining processes has interesting prospects for the future. When these technologies are combined, intricate, lightweight structures with internal lattices or channels can be created that are not achievable with just regular CNC machining. This provides opportunities for even more high-performance and fuel-efficient aircraft designs.
- Cutting-Edge Materials Take the Lead:
The frontiers of what is conceivable are continuously being pushed by developments in material science. CNC machining will welcome the introduction of even stronger, lighter, and more heat-resistant materials in the aircraft production process. Imagine developing vital engine parts out of titanium alloys of the future or investigating the possibilities of composites with even higher strength-to-weight ratios.
- Real-time monitoring and cloud-based manufacturing:
CNC machining will probably become more integrated in the future. Cloud-based manufacturing platforms will make remote diagnostics, predictive maintenance, and real-time machine performance monitoring possible. This translates into lower downtime, more operational efficiency, and the capacity to fine-tune machining procedures for even better outcomes.
Accepting a Better Future:
CNC machining will remain a key component in the development of aircraft production by adopting these innovations. This will lead to the development of lighter, more fuel-efficient, and eventually sustainable aircraft, opening the door to a more promising future for aviation.
Conclusion:
Huayu Prototype provides the best solutions for all needs related to low-volume manufacturing and rapid prototyping thanks to years of manufacturing experience. We reduce the invention cycle to four simple but incredibly powerful phases.